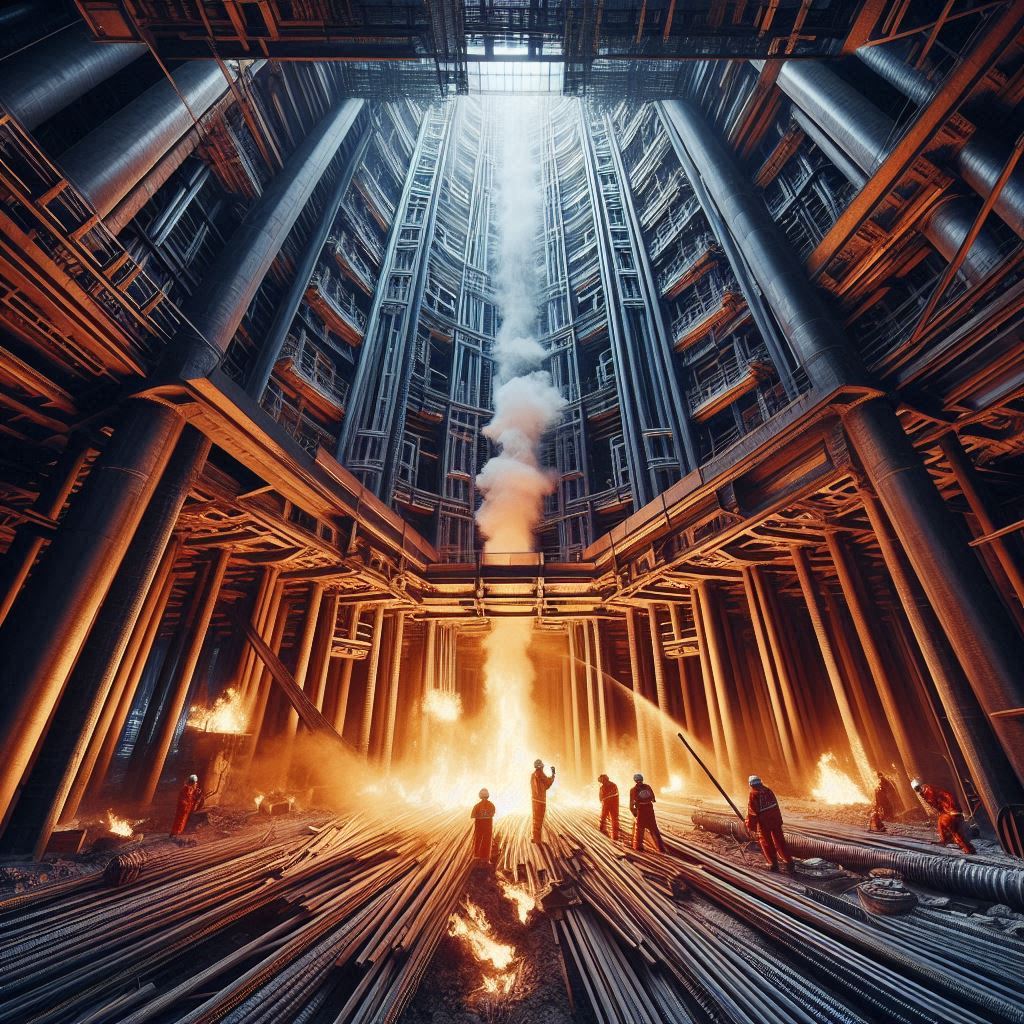
Steel structures form the backbone of modern construction. But they are prone to fire. Heat weakens steel fast. At high temperatures, it loses strength and could collapse at any time. Steel structure fireproofing methods exist to prevent this weakness. These techniques buy crucial time during fires. This is because they allow safe evacuation and emergency response. The right approach depends on several factors. Building use, budget, and aesthetics all matter.
Fire protection codes set minimum standards. Smart designers exceed these. They consider long-term value. Passive fire protection systems work without human intervention. Active fire suppression methods require triggering mechanisms. Intumescent coatings expand when heated. This combination creates comprehensive safety. Let’s explore the best ways to protect steel from fire damage.
Fireproofing Materials: What Works Best
Concrete encasement offers reliable protection. It’s been used for decades. Tough and durable. Spray-applied materials provide another option. They’re faster to install. Gypsum-based products work well for interior columns. They are lightweight and affordable. Mineral wool wraps create excellent insulation barriers. Their fibrous structure traps air. This slows heat transfer.
Vermiculite and perlite concrete remain popular choices. They combine strength with lower weight. Steel structure fireproofing systems must meet specific ratings. These ratings indicate survival time in standardized fire tests, as each building has different requirements.
Cementitious coatings blend cement with lightweight aggregates. They spray directly onto steel. No special skills are needed for the application. Just clean surfaces first. Maintenance remains minimal after installation.
Application Techniques for Maximum Protection
Proper application determines effectiveness. Surface preparation matters most. Remove oils, dirt, and loose materials first. Apply primers where needed. Follow manufacturer instructions exactly. Thickness must meet design specifications. Too thin won’t protect. Too thick wastes money.
Spray applications work well for irregular shapes. Complex beam connections need special attention. Board systems install faster on flat surfaces. They create clean, finished appearances. Contour matching matters for exposed architectural elements.
Quality control involves thickness testing. Inspectors use specialized gauges. They check random spots throughout the structure. Documentation proves compliance with codes. Records protect owners and contractors alike.
Boxed systems encase beams completely. Prefabrication speeds installation. These systems arrive ready to install. Workers need minimal training. This reduces labor costs significantly.
Performance Considerations in Real-World Conditions
Environmental exposure affects durability. Exterior applications need weather resistance. Interior systems face different challenges. Mechanical damage from daily operations threatens protection. Repair procedures should be established early.
Buildings expand and contract. Steel structure fireproofing must accommodate movement. Flexible systems prevent cracking during normal building shifts. Temperature fluctuations test system integrity daily.
Compatibility with other building systems matters. Fireproofing must work alongside electrical, plumbing, and HVAC components. Penetrations require special detailing. These areas often fail first during fires. Proper sealing prevents disaster.
Testing verifies real-world performance. Standard tests expose materials to controlled fires. Temperature curves simulate actual building fires. Pass/fail criteria measure structural integrity. Independent certification proves claims. Don’t trust unverified products.
Maintenance Requirements for Long-Term Safety
Inspection schedules ensure continued protection. Here are some maintenance tips to follow-
- Look for physical damage.
- Check for water intrusion.
- Test adhesion periodically.
- Repairs should match the original materials.
- Document all maintenance activities.
- This creates liability protection.
Renovations present special challenges. Existing fireproofing often gets damaged, where replacement must match the original performance. Sometimes, upgrades become necessary because codes change over time or older systems may not meet current standards.
Fire protection represents an investment. Initial costs seem high. But compared to potential losses, they are minimal. Human lives, property value, and business continuity—all depend on proper steel structure fireproofing. The stakes couldn’t be higher.
Read Also: Next-Generation Barriers: Breaking New Ground in Fire Protection Technology